随着自动化、信息化技术的快速发展,
反应釜温度控制系统正经历着深刻的技术变革。研究反应釜温控技术的最新发展趋势,对于提升化工生产过程的控制水平和经济效益具有重要意义。
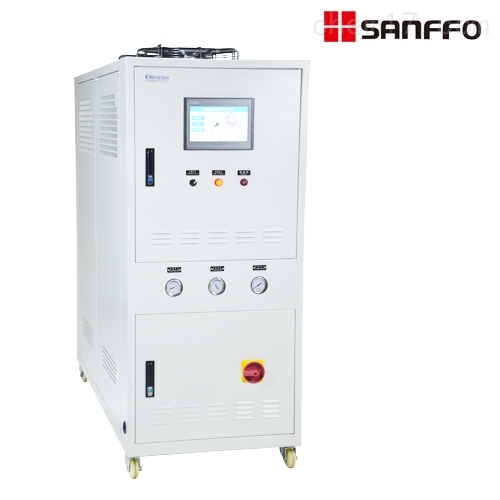
一、传统温控技术的局限性
传统的反应釜温度控制主要采用PID(比例-积分-微分)控制算法,虽然结构简单、易于实现,但在处理复杂工况时表现出明显不足。首先,PID控制对非线性、大滞后系统的控制效果欠佳,难以适应反应釜中常见的时变特性。其次,传统控制方法依赖于精确的数学模型,而实际化工过程中往往存在模型失配问题。再者,单一的温度控制回路无法有效应对多变量耦合和外界干扰的影响。
此外,传统的传感技术和执行机构也存在响应速度慢、测量精度有限等问题。热电偶等常规温度传感器的动态特性限制了控制系统的响应速度,而气动调节阀等执行机构的死区和滞后现象也影响了控制精度。这些局限性促使研究者开发更先进的温度控制策略和技术方案。
二、现代智能温控技术的发展
为克服传统方法的不足,现代智能温控技术取得了显著进展。模型预测控制(MPC)通过在线优化解决了多变量约束控制问题,大幅提升了复杂反应体系的温度控制性能。自适应控制技术能够自动调整控制器参数,有效应对过程动态特性变化。模糊控制和神经网络等智能算法在处理非线性和不确定性方面展现出优势。
在硬件方面,高精度光纤温度传感器和红外热像仪提供了更丰富的温度场信息,为先进控制策略的实施奠定了基础。智能执行机构如电动调节阀和固态继电器的应用,显著提高了控制系统的动态响应特性。同时,分布式控制系统(DCS)和现场总线技术的普及,为复杂温度控制系统的实现提供了平台支持。
特别值得关注的是,人工智能技术在温度控制中的应用日益广泛。深度学习算法可用于建立更精确的过程模型,强化学习则为实现自主优化控制提供了新思路。数字孪生技术通过虚实结合的方式,为温度控制系统的设计和调试提供了高效工具。
三、未来发展趋势与挑战
反应釜温度控制技术的未来发展将呈现以下趋势:一是控制算法将更加智能化,结合机器学习和专家知识实现自主决策;二是系统架构将向网络化方向发展,借助工业互联网实现远程监控和协同优化;三是控制性能将更加注重能效指标,通过优化控制减少能源消耗。
物联网技术的应用将使温度控制系统具备更强的数据采集和分析能力。通过部署无线传感器网络,可以实现反应釜温度场的监测。大数据分析技术有助于从历史数据中挖掘潜在规律,为控制策略优化提供依据。数字孪生技术将实现物理系统与虚拟模型的实时交互,提升故障诊断和预测性维护能力。
然而,新技术应用也面临诸多挑战。智能算法的实时性要求与现有硬件计算能力的矛盾亟待解决。网络安全问题随着系统网络化程度提高而日益突出。此外,如何平衡控制性能与系统复杂性、如何验证智能算法的可靠性等问题也需要深入研究。跨学科合作将成为推动温控技术发展的关键。